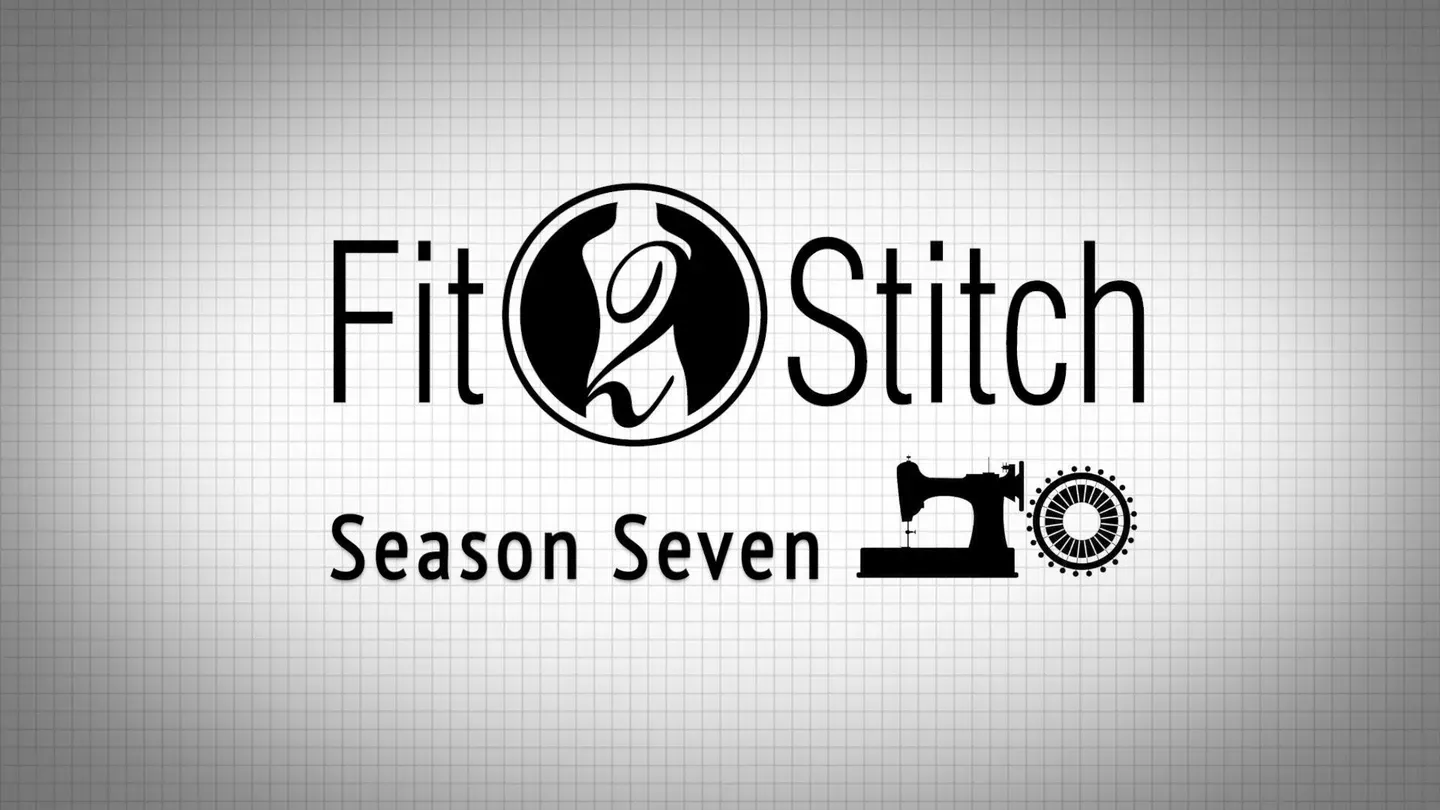
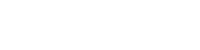
Sewing, Lining, and Fusing the Jacket
Season 7 Episode 708 | 26m 46sVideo has Closed Captions
Continue to make jacket sewing simpler than ever.
We continue to make jacket sewing simpler than ever. Factory methods used today to make a jacket have a factory-made jacket complete in just 3 hours. And remember all of today’s jackets in ready-to-wear are factory made.
Problems with Closed Captions? Closed Captioning Feedback
Problems with Closed Captions? Closed Captioning Feedback
Fit 2 Stitch is presented by your local public television station.
Distributed nationally by American Public Television
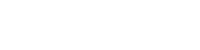
Sewing, Lining, and Fusing the Jacket
Season 7 Episode 708 | 26m 46sVideo has Closed Captions
We continue to make jacket sewing simpler than ever. Factory methods used today to make a jacket have a factory-made jacket complete in just 3 hours. And remember all of today’s jackets in ready-to-wear are factory made.
Problems with Closed Captions? Closed Captioning Feedback
How to Watch Fit 2 Stitch
Fit 2 Stitch is available to stream on pbs.org and the free PBS App, available on iPhone, Apple TV, Android TV, Android smartphones, Amazon Fire TV, Amazon Fire Tablet, Roku, Samsung Smart TV, and Vizio.
Providing Support for PBS.org
Learn Moreabout PBS online sponsorship- Today on Fit 2 Stitch, we continue to make jacket sewing simpler than ever.
Factory methods used today will complete a jacket in just three hours, and remember all of today's jackets in ready-to-wear are factory made.
We'll teach you these methods and clearly explain them, so you can practice once or twice and make great-looking jackets.
You'll be sewing welt pockets everywhere, and all of our new jackets can have a different color lining inside because there are so many great lining choices.
Join us.
(lively music) - [Narrator] Fit 2 Stitch is made possible by Vogue Fabrics, (peaceful piano music) Colorado Fabrics, Quality Sew and Vac, Sew Town, Tulsa, Oklahoma and Fort Smith, Arkansas, Kai Scissors, Sew Steady, Bennos Buttons, All Brands, Cynthia's Fine Fabrics, and Clutch Nails.
- One of my favorite things to do is to be among people who sew.
Quickly, we become friends, and we sit around and chat and talk, and one of my favorite questions, because jackets are a little intimidating, I'll say how long does it take you to make a jacket?
Just estimate, how long does it take you to make a jacket?
And I'll never forget, this woman one time said to me, "A lifetime."
She said, literally, she started on a jacket 10 years ago, and there was parts of it that she just wasn't sure how to do, and she still hadn't completed the (chuckles) jacket.
So, the goal today is really help you.
It will not take a lifetime, in fact, way, way less.
We don't need to put a timer on it, because we want you to enjoy the process, but I think what will help you enjoy that process is if you're confident of how to do the parts.
And with a jacket, if you notice, the devil is definitely in the details.
So let's take a look.
I think there's really three main sections that will really make a difference to us.
The notch lapel, very important.
If it's not (chuckles) right, we'd just, we'll scream homemade, and what we want is not that.
Also, the welt pockets, whether it has a flap, not a flap, we're gonna learn how to do that and do it beautifully, just again, with such detail, but it's very simple.
And also, the notch lapel.
What I need you to notice about a notch lapel, and several people, if they've made jackets, and they'll come in to me and say, "What do you think of my jacket?"
The collar is upside down, and just a lot of women don't know this feature, is that if I close up the jacket, if you notice, the collar itself is always shorter than the neckline.
The neckline of the jacket is longer, and what makes a notch lapel is that the collar actually stops short of the neckline.
So that's important to know, but the next thing I want you to notice is look at the outside edge of the collar is shorter than the neck edge.
Now that is styling, and in some cases, you'll see that that doesn't change, but for today, I want you to notice that the outside edge of the collar is shorter than the neck edge of the collar, so when we go to make that collar, and go to put it on, we'll see exactly that.
If I do close up this collar, again it's styling.
How far close the collar comes to the edge of the neckline, but what makes that notch lapel is always that the collar is shorter than the neckline of the jacket.
All right, so then let's start in with fabric, so it's the first thing I wanna talk about.
There's a very contemporary, we've been doing it for a long time in manufacturing, it's really just that a lot of home sewers don't really understand this concept, and it's that of fusible interfacing.
Because it's called interfacing, we think of it as a spot treatment, and that's not what we wanna do.
We don't want a spot anything.
In manufacturing, they do, but they do it to save money, and the beauty of being at home is we can make it better, especially because the money we're gonna spend is just not that much compared to what it's going to yield us out in the improvement of the product.
So what we're gonna do is we're gonna use fusible interfacing underneath the whole entire body of the jacket.
Not in every case, definitely not in every case, but I do wanna talk about when we're gonna use it and why we're gonna use it, all right?
So there are four main reasons we're going to use fusible interfacing.
The first is when we're simply trying to give body, add body to a jacket.
So this is a jacket I've made.
This was the original fabric.
If I hold it up, you can kind of see it's just almost sheer.
It's got great body, but not for a jacket, so when I take a fabric and maybe use it for something that maybe it's not its most natural intent, I can fuse the whole entire thing, and it gives me the body that I need.
So I'm using an interfacing as an underlining.
If you go back and remember in the old days when there was tissue inside of a gift box, and the whole purpose of that tissue is kind of to retard the wrinkling that was in the garment in the box.
So that's what this fusible does.
It's another layer that simply creates it to be a little more buoyant, give it a little more spring.
When you open up the body of the jacket, you can see that what I did is I fused the whole entire body of the jacket.
So you would never know it by looking at the fabric.
You shouldn't know it, but when I'm trying to add more body, that's a great reason to fuse.
Another reason is if I'm taking a fabric, if it's very loosely woven.
Something very loosely woven like this, if I don't fuse, and I don't have to fuse, but just know that if I don't fuse, it's gonna shorten the life of that jacket, because the fibers are gonna shift to the space where they can.
So I'm gonna look at one of the jackets on the mannequins, and this is a perfect example.
This jacket right here is just like that fabric I showed you on the table.
It's very loosely woven, and it, using that fabric is wonderful for a jacket 'cause it makes a great fringe.
It's just stylish, and it's really a beautiful fabric.
However, knowing that I don't wanna spend the money that I spent on the fabric, and the time that I spent making the jacket, I don't wanna wear it a short period of time, and notice then that the fibers are starting to spread, and there's no way to stop that.
Lining does not stop the fibers from spreading.
That's the job of the fusible.
So if I look inside this jacket, and just peek down at a corner, what you'll see is the whole inside is fused.
And it's very easy to do.
We're gonna go through the process of how to do it, but what I'm saying to you is let's decide when I'm going to use and when I'm not.
So just to go over it, I haven't gone over all four reasons, but the first is when I need to add body.
The second is when I need to stabilize a fiber.
The other reason might be that I want to retard wrinkling, just like that tissue in that box.
And the other reason is not necessarily in a jacket, but sometimes in a blouse, if I'm using a sheer fabric, they will fuse the body of the blouse, but leave the sleeves sheer.
And it's a beautiful contrast.
It's a beautiful look.
I only wanna use black or white fusible.
There's no need to add all the colors.
What I want to do is look at the fabric and figure out what's the closest that will do it.
Sometimes when I put a fusible under a fabric, it actually will change the net result.
So if I were to put white under this brown, versus the black that I did it with, you can see that one has the tendency to lighten the fabric, and the other has a tendency to darken, and there's not a right and wrong.
It's completely our styling and our choice.
We're the designer, and we get to choose what we want, but just recognize that that color underneath may make an impact as to what the final result will be.
All right, so we've got our reasons clear.
I would definitely suggest to you that if you are in doubt, fuse the jacket.
Don't leave it not fused, if in doubt.
I did bring an example, and I wanted to show you this particular fabric.
This is just a beautiful piece of fabric.
If we look back at the jackets, this is the jacket that I did on the first mannequin.
And I just absolutely love this jacket.
I'm gonna take a little peek inside, and when I did this and made this, there's not anything, there's nothing.
There's no fusible, there's no interfacing, nothing inside of that jacket.
It's just absolutely simple and easy.
If you are first-time making jackets, and you feel like this fusible is too much, just look for a fabric that's naturally beautiful that you wouldn't need to add a layer into it, but I will tell you that when I first starting making jackets, because I was very intimated by making jackets, I decided that the fusible actually helped me.
It helped the edges not fray out.
It just helped a little bit, and I got to where I was using fusible for everything, and then as I got better at jacket-making, I peeled away from it a little bit as my sewing skills improved.
So I think if you recognize that it helps you make a jacket, you'll have a tendency to use it as an aid in the beginning, and then peel away from it.
When we cut out our jacket, I wanna show you something, and then we'll show you the fusible, but I do wanna show you something that's very common in the industry.
Now keep in mind that when the industry cuts out, they're laser cutters, and the fabric is pressed down, and the big laser cutters come around.
The beauty of those laser cutters is they are accurate, and one of the things a laser cutter will do, and I'm gonna show you here is it does what's called a crosscut, so it will cut this way, and sometimes when that happens, the weight is distributed differently.
It'll release the pressure.
It'll come back down, so that everything relaxes, and you can cut this way.
So it is called crosscuts, and what that does is it gets a very accurate corner.
Again, let it relax.
You can see that if it slipped a little bit, cut this way, and then you'll see that that is as close to the tissue as it possibly can be when we go to do those crosscutting on the sections.
It's especially important as you get up to the neckline, and the armhole, and the shoulder, where those little differences make a little bit more of a difference in the end result.
And really all we're doing here is being accurate.
Accurate is really the name of the game.
This fabric I'm gonna fuse, it's a lightweight.
I'm going to decide that I'm going to fuse it.
I'm not sure, first off I have to decide which side is the right side.
I'm gonna say this is the right side, so I'm gonna give you a little tip here that will really save in your process of fusing.
I'm gonna put right sides of my fabric together, and then I'm gonna put right sides of my fusible together.
So what that means is I can lay out my fusible and my fabric all at the same time.
I don't want you to have to cut your fusible separate, and you're gonna fuse all your fashion fabric body pieces.
So that means the body itself, the collar, the welts, all of that.
I don't fuse my lining.
Everything else I do.
So I'm going to now cut this.
Now remember what I did is my fusible is right sides together, so that means the glue is to the outside.
And I'm gonna cut this piece, and cut it all at the same time.
And I'm just gonna do a little sample because I really just want you to see kind of how this works and how you can simplify it.
Again, do my crosscuts, and I've got a fold down here, and I'm gonna eliminate that fold.
Just in this case, we don't have a fold.
Okay, so now I've got it.
I've got two layers of fusible.
I've got two layers of fabric.
Let's go to the iron.
I'm gonna show you how to press this all together.
All right, leave it just like this, once I get to my iron.
And what I wanna do is just leave the whole stack.
Just peel off the back layer.
Now the reason I'm doing this because what I know is this layer now is already on the wrong side of the fashion fabric, so I've got the glue against the wrong side of the fashion fabric, and I'm just gonna give it my steam.
(seam hisses) You don't worry about your fusible interfacing.
That is low-temp fusible.
That's not gonna be my concern.
My concern is I set my iron temperature to whatever is the temperature of my fashion fabric.
So if you notice that's fused, you know everyone always says 10 seconds.
I don't even know if 10 seconds is necessary.
Feel what side is the glue side.
Put the glue side down.
The glue side has the little bumps on it.
The other side is smooth and easy, (steam hisses) and then I can go and just give it a little bit of steam.
And there what you notice is everything holds together so much better.
I think it's magic.
I love it (chuckles).
All right, but let's get into the body of the jacket, because what I really wanna show you now are keeping those details really crisp and clean.
All right, so let's start with the collar.
Remember when I said to you that the collar edge is longer than the outside edge.
So I've cut this sample here, and the way we're gonna do it is we're gonna put this together, right sides together.
You'll have an upper collar and an under collar.
That's not a big deal, but I want you to see that what I'm gonna do is I'm actually gonna sew across the edges, and what I don't want you to do is leave your needle down and change directions.
It's a really (sighs), I don't know, we're gonna call it dated.
It's a really dated method, because by just like when we did our cutting, if we do that with our sewing as well, we'll see that our stitches will actually cross one another, and they'll just give us a nice sharp corner there.
And then what we can do is we can turn it, and turn it, and I'm gonna do this on both ends.
I'm just sampling this one side, and when I hold it there and turn the edge, even without pressing, you see what a nice sharp corner I get.
You just can't get it any better.
So that's the first step I'm gonna do when I create my collar.
Then what I've done is I've actually turned the collar, and I've sewn it on to the neckage of my jacket.
Again, you notice that this is the longer edge.
This the shorter edge.
If you don't pay attention to those notches, it's so easy to flip it around.
I can't tell you how many times I've seen collars that are upside down, and not anyone notices, but you know, that's hey, that's what I notice in life, okay (chuckles)?
So then we're gonna come along with the facing.
When I put the collar on, I just baste it in place, and a very important thing to do is to make sure that the collar ends the same distance from the front of that jacket.
And again, it's very simple to do.
I just need to pay attention to that detail, because then what I'm gonna do is I'm gonna come along with my facing, and I'm gonna put my facing right on top.
And in this particular case, there it is, right on top, and I'm just gonna sew a small section of this because you'll get it when I sew that small section.
The rest of it is just really simple to do.
I did use a contrasting collar, and I've used contrasting thread so that you can really see the differences here.
So I would start at the bottom, come all the way up, and then what I'm gonna do is sew right off the edge.
Remember this is what I was talking about.
Don't leave your needle down and change directions.
It's going to just not give you as nearly as neat of a corner as if I leave the needle down and change directions.
(sewing machine whirs) All right, so now what I'm doing is my facing, I'm sewing through all the layers.
My collar's in between, and I just continue all the way.
So I'm sewing from the bottom up, across the neckage, and back down the other way.
It doesn't matter which one I sew first.
None of that makes a difference.
So there I can see my red stitching, and I can see where my corners are crossed.
So I'm gonna do the same thing.
I'm gonna fold.
I'm gonna fold.
I'm gonna flip it to the outside, and we are going to have this most beautiful, spectacular notch lapel, because what you'll see is it's not formed by crossing, crossing, crossing, or turning.
It's formed by actually, just inserting that collar in the way.
Now here would be probably longer.
You know that's all styling, but you can see how clean those corners are and how beautiful anyone can do notch lapels, as long as you have straight sewing abilities, which I know you have.
Let's do a sleeve, all right?
Let's do a sleeve.
The goal on our sleeve is to ease up that sleeve to where it looks absolutely beautiful inside.
So I've noticed in sewing there's some terms that sometimes they're used synonymously, and they're not.
So two of those terms that I've noticed are easing and gathering.
And easing and gathering are not the same thing.
So just to clarify, gathers are when I want the fullness or the extra fabric to actually be visible.
I literally will see little tiny collection of extra fabric poking out.
Easing is when I have more fabric, so the sleeve is eased into the armhole.
Why, because it makes it easier to move.
My mobility goes way up.
However, I don't want that to show, and when it does show, it doesn't look good.
In fact, it looks kind of homemade.
So there is a product that we're gonna use that's just really easy.
In fact, they use it inside of men's neckties.
Let me show you what it looks like, even.
It looks like a necktie, because the edges of a man's necktie are never pressed.
They're nice, they're soft, they're just always crisp, and that's what we want our sleeve caps to be.
So that's why, in this particular case, I've cut a bias.
And the reason I use a bias is it stretches, and then it retracts itself.
That's what we need in easing, so along the top of this sleeve cap, from the notch up and back to the notch, we don't need it down here because this is a one-to-one ratio, I'm actually going to put the tie interfacing on the inside of the sleeve.
I'm going to turn my machine to baste, and for you guys, just make that as long as it will be.
My machine's going to a six, whatever your longest machine stitch is.
And right on my seam allowance, now I'm gonna suggest for everyone, I don't care what pattern you're using, get your seam allowances down to 3/8.
The reason being if you're trying to use 5/8, you've got a convex and a concave.
Your armhole is concave.
Your sleeve is convex.
And so, actually that's opposite.
Your sleeve is concave, and your armhole, whatever it is, you'll get it, but when I try to add seam allowances to both of those lines and put them together, it just doesn't work well.
The seam allowance actually gets in my way.
So both on the sleeve and the armhole, I'm gonna have you reduce the seam allowance down to 3/8.
So now, I'm right there.
My seam allowance is 3/8, and I'm actually gonna pull, once I get it sewing, I'm gonna pull this tie interfacing.
Now if you pull too hard, your machine won't go forward.
(sewing machine whirs) So don't pull too hard.
Just make sure that you have some tension to it, and you wanna make sure that tension is consistent and even as you go across, as you go all the way around from notch to notch.
Once I do that, and what you're gonna see, what happens is that creates that beautiful sleeve cap, and if you notice there's not a single gather, and I can't gather this sleeve.
It's not possible to gather this sleeve, and that's the beauty of doing this extra.
Now the good news is, too, is what happens is I set that sleeve in.
Again, I'm gonna put the sleeve down against the machine because the feed dogs are pulling in the largest part of my sleeve, and so put the sleeve down.
Now I know that's gonna be different for many of you, but put that sleeve down, and it will make all the difference.
But I'm going to, once I put it in, the sleeve cap, the tie interfacing, will become my sleeve cap, and that's a good thing.
Perfect, let's look at welt pockets, probably my favorite, only because once you learn them, oh my gosh, you guys.
I've got welt pockets on my towels at home, because it's so exciting to do welt pockets.
So I'm gonna show you the first step, and then I'll kind of take you through what I've already done, just so that you don't get too, you know, just to make it simple.
There's three steps.
You guys can do this.
It's very simple to do.
I've taught it over and over, and you know what, everyone gets it.
I'm gonna start off with strips that are one-inch wide and eight inches long.
Most welt pockets are six inches finished, but I want an inch on each end, just to make it easy to hold on to, and I think that's what's gone wrong with other pockets, but we're gonna make it eight inches by one.
I'm gonna press 'em and fold them in half.
Most of the time I'll fuse these strips, even if I'm not fusing the whole jacket, I'll fuse the strips 'cause I think it gives me a little extra body, and what I'm gonna do is I'm gonna put them wrong sides together, and I'm gonna stitch right down the center.
And if you notice here, I've stopped and started right in the same place.
Stop, backstitch, go.
Start backstitch, then I've cut.
This is a big difference.
This will make a big difference.
See how long that triangle is.
That triangle makes it so much easier, because what I can do now is I'm gonna flip those to the inside.
And if you cut right to that point, which is why good scissors are so important, that pocket, that flap, will just flip right to the inside.
Then I come along, and I put my pocket, and I'm gonna do this for you so you can see it.
I put my pocket right behind the flap, so my pocket I've done different fabrics here.
It's all gonna be the same fabrics.
Don't do different fabrics.
It's all gonna be the same, but I'm gonna put that right behind it.
And the clue that you'll have is you notice when I cover the hole, notice the pocket piece is covering the hole.
And when I cover that hole, you notice I can't see the stitching line that I've stitched previously, so turn it on this side and start there.
I'm gonna start right there at the edge, and I'm actually gonna stitch right on that line, all over again.
Now what that would do is it'll actually, it'll reinforce the welts, and when I look at it, you guys, it's gonna be so pretty.
It'll reinforce the welt, but it'll also create the pocket piece, and then I can either make it one piece and sew it to the other side, exactly the same.
So my first step is sewing the two welts, even, but what I love about it is if they're not even, I haven't done anything.
I haven't cut the jacket yet.
Don't cut the jacket until you're sure they're even, until you're happy with the way they look, and then you're good to go.
Then I attach my pocket, easy, again just two strips.
The very last thing I do is I bring this corner up, and notice that big triangle just hanging there.
That's when I come, and again, with those crosscuts and those cross-sewing, I can make that welt so precise and so accurate that I just love 'em.
And there's all kinds of things we can do with them.
We can add a flap later on, as you gain confidence.
You just slip a flap right up in there, across the edge, and it just looks absolutely beautiful.
And you will love jackets-making as much as I will, and I don't think there's any area where we can save more money is with jackets.
It's awesome.
Next time, we're gonna talk about probably one of my favorite and most-needed subjects ever, because I absolutely needed this more than you do, and I only put it in here for myself (chuckles).
So it is accessories, and what I love about accessories is accessories.
And what frustrates me about accessories is kind of how to use them, and how to organize them, and how to do all of that.
Carrie Bradshaw has said, "I like my money, "right where I can see it, hanging in my closet."
Accessories and how to organize those closets, next time on Fit 2 Stitch.
(peaceful piano music) - [Narrator] Fit 2 Stitch is made possible by Vogue Fabrics, Colorado Fabrics, Quality Sew and Vac, Sew Town of Tulsa, Oklahoma and Fort Smith, Arkansas, Kai Scissors, Sew Steady, Bennos Buttons, All Brands, Cynthia's Fine Fabrics, and Clutch Nails.
(lively flute music) To order a four-DVD set of Fit 2 Stitch Series 7, please visit our website at fit2stitch.com.
Support for PBS provided by:
Fit 2 Stitch is presented by your local public television station.
Distributed nationally by American Public Television